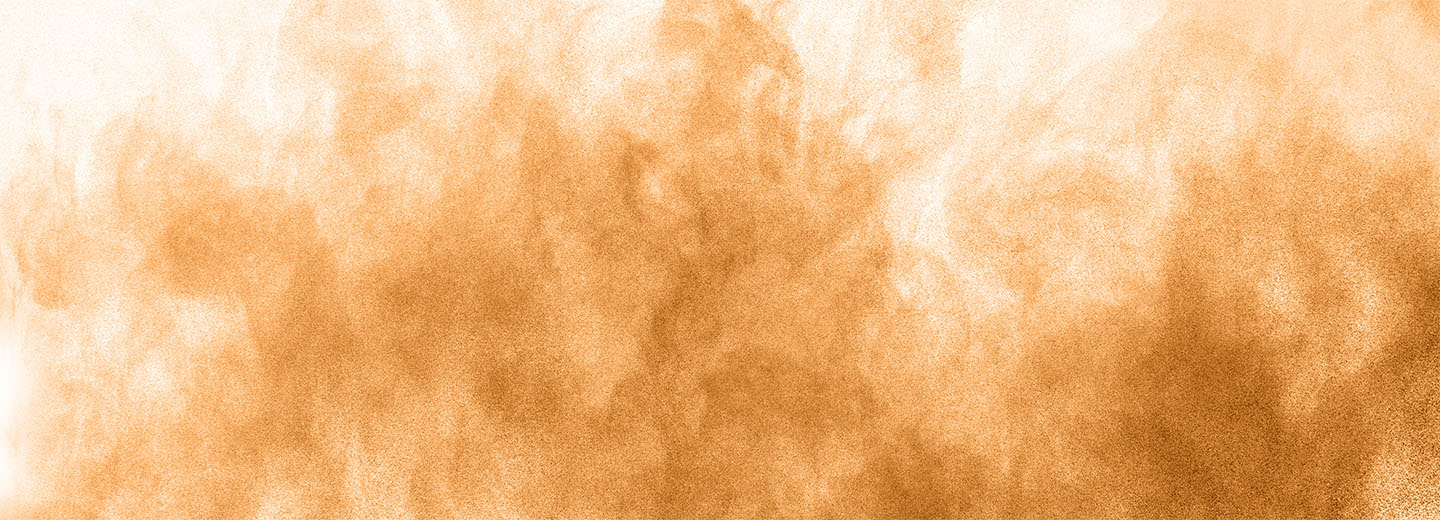
Vacuuming and dust removal cover all the techniques used to capture, filter and eliminate the dust in the air. They guarantee a healthier, safer and more efficient working environment.
Read more
Looking for a filter, an application, an accessory?
E-Catalog
CATALOG.HIFI-FILTER.COM
03.09.2024
06.05.2025